What is Reject?
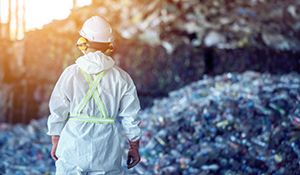
Reject is also known as waste or defective production and refers to the parts produced that did not meet quality standards at the first check. In the Six Big Losses, reject parts occur in either the steady-state production or during a start-up after a downtime event (reduced yield).
In addition to the information you provided, here are some additional details about rejects in production:
- Rejects can be caused by a variety of factors, such as equipment malfunction, operator error, or material defects.
- The cost of producing rejects can be significant, including the cost of materials, labor, and lost production time.
- Rejects can lead to downstream quality issues if they are not caught and addressed early in the production process.
- In some industries, such as pharmaceuticals or aerospace, the cost of a single reject can be extremely high due to the potential impact on safety or reliability.
- Implementing quality control measures, such as statistical process control or root cause analysis, can help reduce the incidence of rejects in production.
Reject parts can be obtained by subtracting the actual (good) production from total production.
Reject Formula
Reject = Total Production - Actual (good) Production
Rejection Rate Formula
Rejection rate(%) = (Waste Material Cost ÷ Total Cost of Production) × 100%
OR
Rejection rate(%) = (Total Units/Quantity of Waste Materials ÷ Total number of units/quantity produced) × 100%