What is a Reason Code?
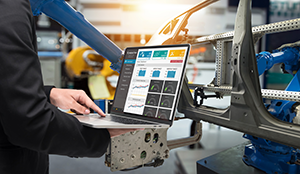
To assess and keep records of the underlying causes of manufacturing problems, reason codes are implemented throughout the application to streamline reporting.
A reason code consists of three levels: Top Level, Level 1 and Level 2, which provide an accurate drilldown of the issues that can occur during a shift on-site related to performance, availability or quality failure.
Reason codes are used in various industries, including manufacturing, to identify the root causes of problems and streamline the reporting process. By assigning codes to specific issues, companies can quickly analyze and categorize the problems that occur during production, and develop strategies to address them. Reason codes help companies to identify the most common issues that occur during production, as well as the areas that require improvement.
The three levels of reason codes provide a detailed analysis of the problems that occur during a shift. The top-level code provides an overview of the problem, while Level 1 provides a more detailed description of the issue. Finally, Level 2 provides a comprehensive analysis of the issue, including the specific cause of the problem. By using reason codes, companies can quickly identify the underlying causes of problems and develop effective solutions to address them.
Overall, reason codes are an essential tool for companies that are looking to optimize their production processes. By accurately identifying the root causes of problems and streamlining the reporting process, companies can increase their efficiency, reduce downtime, and improve the overall quality of their products. Reason codes provide a structured approach to problem-solving, which allows companies to make informed decisions based on accurate data.
Shift managers and other reporting personnel can add reason codes to state the reason for a series of rejects, unplanned or planned downtime, and any other occurrence that hinders with the optimal production process.