What is an Unplanned Downtime?
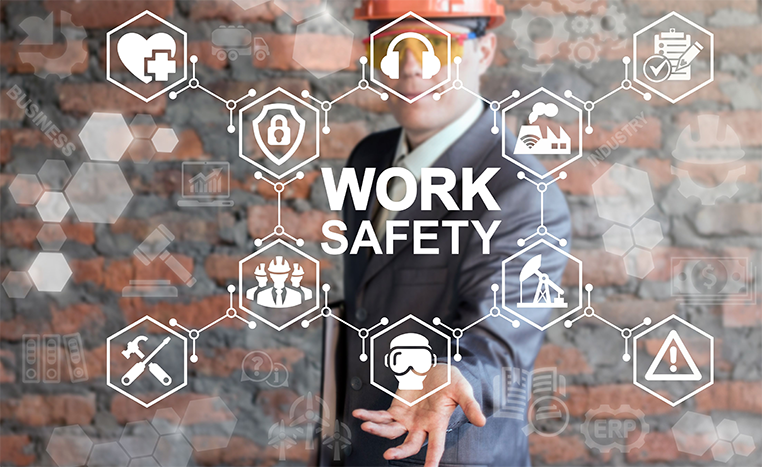
Unplanned Downtime is referred to any duration of time when the production process is scheduled to be running but is not due to reasons such as equipment (machinery) failure or shortage of raw material. Unplanned Downtime forms a part of Availability Loss in the OEE calculations.
Unplanned Downtime can have a significant impact on a company's bottom line. The loss of production can result in reduced output, delayed shipments, and ultimately, decreased revenue. Additionally, unplanned downtime can lead to increased maintenance costs, as equipment may need to be repaired or replaced more frequently due to unexpected failures.
Effective maintenance strategies, such as predictive maintenance and condition-based maintenance, can help companies minimize the impact of unplanned downtime. By monitoring equipment performance and predicting potential failures, maintenance teams can proactively address issues before they result in production downtime. Regular equipment inspections and maintenance can also help identify potential issues before they become larger problems.
In addition to impacting production and profitability, unplanned downtime can also harm a company's reputation. Late deliveries and reduced product quality can damage customer relationships and result in lost business. Furthermore, unplanned downtime can create safety hazards in the workplace, as equipment failures or malfunctions can lead to accidents or injuries. Therefore, it is crucial for companies to prioritize maintenance and take proactive measures to minimize unplanned downtime.
Overall, managing unplanned downtime is crucial for ensuring optimal production output and profitability. By implementing effective maintenance strategies and closely monitoring equipment performance, companies can minimize the risk of unplanned downtime and avoid the negative impacts on their operations.