What is Equipment Failure?
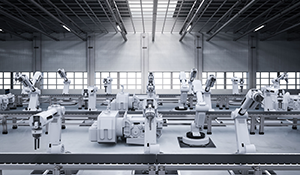
Equipment failure is a common occurrence in manufacturing industries and can have significant impacts on production output and operational costs. Unplanned maintenance can be a major contributor to equipment failure, as it often requires the shutdown of the entire production line, resulting in costly downtime. In addition to the direct costs associated with equipment repairs and replacement, equipment failure can also result in lost revenue due to missed production targets and delivery deadlines.
Preventative maintenance is crucial for minimizing the risk of equipment failure. Regular inspections, cleaning, and lubrication can help identify and prevent potential issues before they lead to downtime. It's also important to have a plan in place for responding to equipment failure, including spare parts inventory, emergency repair services, and contingency production plans. By taking a proactive approach to equipment maintenance and repair, businesses can reduce the risk of equipment failure and minimize its impact on their operations.
In today's fast-paced manufacturing environment, equipment failure is a critical challenge that needs to be managed effectively. Businesses that invest in modern equipment monitoring and predictive maintenance technologies can minimize the risk of equipment failure and optimize their production efficiency. These technologies enable real-time monitoring of equipment performance, detecting potential problems before they cause downtime. With predictive maintenance, businesses can also plan equipment maintenance around their production schedules, minimizing the impact on production output and improving overall operational efficiency.
It refers to any equipment scheduled for production during a given time not functioning due to some sort of failure. Equipment failure also makes a significant part of unplanned downtime (stops), and hence causes an availability loss. Examples of equipment failure are unplanned maintenance, tooling failures, and machinery breakdown.