What is Availability in OEE?
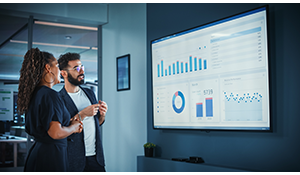
Availability is one of the three OEE factors that considers Availability Loss, which refers to any event(s) that halt production for any length of time. Examples of Availability Loss are planned and unplanned downtime (stops), including changeover time.
Availability in OEE (Overall Equipment Effectiveness) refers to the percentage of time that a manufacturing process or equipment is available and operating during scheduled production time. It takes into account any planned or unplanned downtime, such as maintenance, changeovers, or breakdowns.
To calculate Availability, you need to divide the actual operating time of the equipment by the scheduled production time, and then multiply the result by 100. For example, if a machine was scheduled to run for 8 hours but experienced 2 hours of unplanned downtime, the Availability would be 75% (6/8 x 100).
By measuring Availability as part of OEE, manufacturers can identify the reasons for downtime and implement strategies to minimize it. This can lead to increased productivity, reduced costs, and improved customer satisfaction.
An Availability score of 100% means that the manufacturing unit is running with no downtime.
Availability = 100 X [ Uptime/ (Uptime + Downtime) ]