What is Availability Loss?
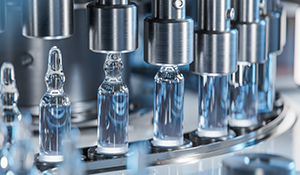
Availability Loss refers to the events that interrupt or stop regular production activities for any length of time, such as planned and unplanned downtime. Availability Loss also takes into account for OEE calculation changeover time, since manufacturing activities could have been carried out in that period otherwise
In manufacturing, availability loss can have a significant impact on productivity and profitability. It can occur due to a variety of factors, such as equipment breakdowns, scheduled maintenance, or unexpected downtime. The cost of availability loss can be substantial, not just in terms of lost production time but also in the resources required to get production back up and running. To mitigate the risk of availability loss, many manufacturers implement proactive maintenance programs, invest in quality equipment, and regularly monitor production processes to identify potential issues.
One way to measure the impact of availability loss is through Overall Equipment Effectiveness (OEE). OEE is a performance metric that calculates the percentage of time that a machine or production line is running at optimal capacity. Availability loss is one of the three factors that contribute to OEE, along with performance loss and quality loss. By tracking OEE, manufacturers can identify areas where availability loss is occurring and take steps to minimize its impact on productivity. Additionally, analyzing OEE data can help manufacturers make informed decisions about when to schedule maintenance and identify opportunities to improve production efficiency.
Finally, availability loss can have a ripple effect throughout the supply chain. For example, if a manufacturer experiences significant downtime due to equipment failure, this can cause delays in production schedules and lead to missed delivery deadlines. In turn, this can impact the manufacturer's customers, who may need to adjust their own production schedules or find alternative suppliers. To mitigate the impact of availability loss on the supply chain, manufacturers can invest in redundancy and contingency plans, such as backup equipment or alternative suppliers, to ensure that they can continue to meet customer demand even in the event of unexpected downtime.
Scheduled Run Time = Scheduled Production Time - Availability Loss