What is Downtime?
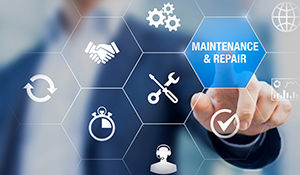
Downtime can be categorized into two types: planned downtime and unplanned downtime. Planned downtime is a pre-scheduled event that takes place during a manufacturing process, often for maintenance, repairs, or upgrades. In contrast, unplanned downtime is an unexpected interruption that can occur due to various reasons, such as equipment breakdowns, power outages, or labor shortages. Unplanned downtime can have a significant impact on the manufacturing process, leading to loss of productivity, revenue, and customer satisfaction.
Downtime can be a costly problem for any manufacturing business. It not only affects the production capacity of the company but can also lead to higher operating costs, longer lead times, and lower product quality. In addition, downtime can affect the morale of the workforce, leading to decreased motivation and productivity. As such, manufacturers must adopt proactive measures to minimize downtime, including regular equipment maintenance, monitoring and analysis of production data, and the implementation of robust contingency plans to deal with unexpected disruptions.
To address the issue of downtime, many manufacturers are adopting new technologies such as predictive maintenance, automation, and machine learning algorithms. These technologies enable manufacturers to predict equipment failures and take preventive measures before a breakdown occurs. Additionally, automation can reduce the need for manual labor and improve the accuracy and efficiency of the manufacturing process. By leveraging these technologies, manufacturers can reduce downtime, improve productivity, and stay ahead of the competition.
Downtime or Stop Time refers to any duration where the manufacturing process was meant to run but was not due to unplanned or planned stops. Such stops lead to Downtime Loss.