How To Create a Planned Downtime?
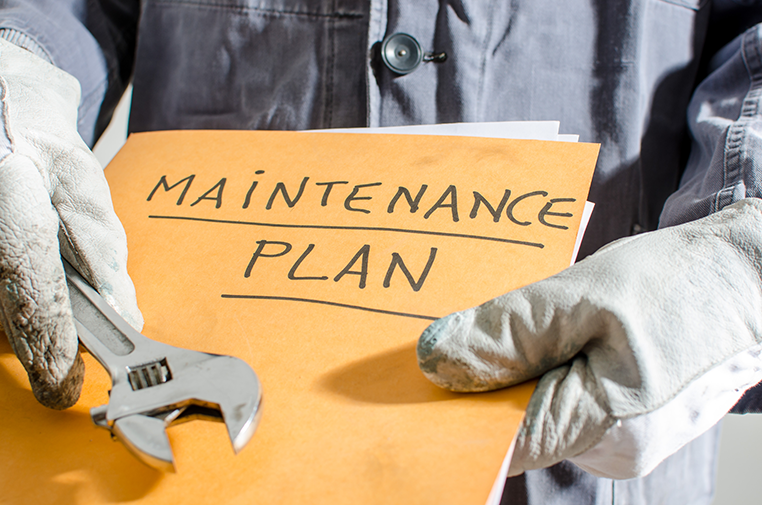
In a few simple steps, you can start a planned downtime and add the reason or equipment involved.
Practice the steps as shown and you'll learn how to go about the add downtime panel like a pro!
Steps:
-
Click on the Planned Downtime card on the first panel.
-
In Step 1, select the Start and End date-time on the date and time picker. To add the end time, you can use the calendar or duration tabs.
-
In Step 2, specify a downtime reason code. For unspecified downtime reasons, click “Reason code is not known yet.”
-
If the cause for downtime is known, click “select.” The Reason Code panel will open.
-
Add a reason code by choosing from the lists provided in Top Level, Level 1, and Level 2. Click “Select Reason Code” to save.
-
(Optional) Add more details regarding the downtime in the comment box.
-
Select equipment (if necessary) by clicking “Tag equipment”. Click on equipment from the options or Click “Add a tag” to mention unlisted equipment.
-
Click Add Downtime. There you go, all done!
Validation Rule:
-
The end date time must be greater than the start date time for downtime.
Helpful Tips:
-
Add an unspecified/unknown downtime reason code by clicking “Select” under Select Reason Code. Click “Unknown/Unspecified” under Top Level and click “Select Reason Code”.
-
The system will run a validation test and ask for corrections if need be. Once the planned downtime is validated, the data will be recorded.