What is Ideal Cycle Time?
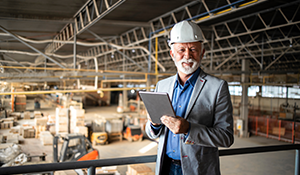
Ideal Cycle Time is the theoretical time taken to produce one part and is used in the calculation of Performance in OEE. Ideal Cycle Time is the inverse of Ideal Run time.
In manufacturing processes, Ideal Cycle Time refers to the amount of time it would take to produce a single unit or part if all conditions were perfect. This includes factors such as equipment performance, operator proficiency, and material availability. The Ideal Cycle Time is a critical metric in measuring the efficiency and productivity of a manufacturing process. It helps in identifying areas for improvement, reducing waste and optimizing the overall process.
The calculation of Ideal Cycle Time is essential for determining the Ideal Run Time, which is the maximum time that a process should take to produce a part. Ideal Run Time includes factors such as planned downtime, changeover time, and maintenance time. By understanding and optimizing Ideal Cycle Time and Ideal Run Time, manufacturers can reduce the time and cost of production while maintaining high levels of quality and consistency.
In addition to calculating the Ideal Cycle Time and Ideal Run Time, manufacturers use Overall Equipment Effectiveness (OEE) as a key performance indicator to evaluate the performance of their production processes. OEE measures the percentage of time a machine or production line is working efficiently, producing quality products, and meeting production goals. The Ideal Cycle Time is a critical component in the calculation of OEE, as it represents the optimal time it should take to produce a single part.