What is Reduced Speed?
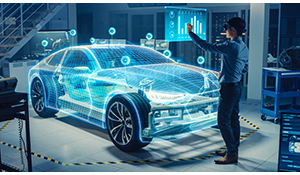
Reduced speed is a significant issue that can affect the overall efficiency and productivity of manufacturing processes. When equipment runs at a slower speed than the ideal cycle time, it can lead to longer lead times, reduced output, and increased costs. This can result in lower customer satisfaction, lost sales, and decreased profitability. Therefore, it is essential to identify the root causes of reduced speed and take corrective actions to mitigate its effects.
One way to prevent reduced speed is to conduct regular equipment maintenance and replacement. Proper maintenance ensures that equipment operates at optimal performance and minimizes wear and tear, reducing the chances of breakdowns and repairs. Additionally, upgrading to newer equipment can increase operational efficiency and reduce cycle time, resulting in higher productivity and profitability.
Another way to prevent reduced speed is to improve the overall work environment. Poor line environment, such as inadequate lighting, poor air quality, and high noise levels, can lead to reduced operator performance and equipment malfunction. By providing a safe and comfortable work environment, operators can focus on their tasks, which leads to higher efficiency, improved output, and reduced downtime due to reduced speed.
This refers to the event when equipment runs at speed lower than the Ideal Cycle Time. Reduced speed is also known as a slow cycle and is a performance loss. The causes for reduced speed can be poor operation, worn-out machinery, low-quality material, electrical problems, shutdowns, and poor line environment, among others.